The Scientific Research Behind Porosity: A Comprehensive Guide for Welders and Fabricators
Recognizing the intricate devices behind porosity in welding is crucial for welders and fabricators striving for impressive workmanship. From the structure of the base materials to the intricacies of the welding procedure itself, a wide range of variables conspire to either worsen or minimize the visibility of porosity.
Comprehending Porosity in Welding
FIRST SENTENCE:
Exam of porosity in welding exposes crucial understandings into the honesty and top quality of the weld joint. Porosity, identified by the presence of cavities or voids within the weld steel, is an usual worry in welding procedures. These gaps, if not appropriately attended to, can jeopardize the architectural stability and mechanical residential or commercial properties of the weld, bring about possible failures in the completed product.
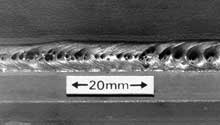
To detect and evaluate porosity, non-destructive screening approaches such as ultrasonic screening or X-ray inspection are commonly utilized. These strategies enable the recognition of inner problems without endangering the stability of the weld. By assessing the dimension, form, and distribution of porosity within a weld, welders can make informed choices to boost their welding processes and attain sounder weld joints.
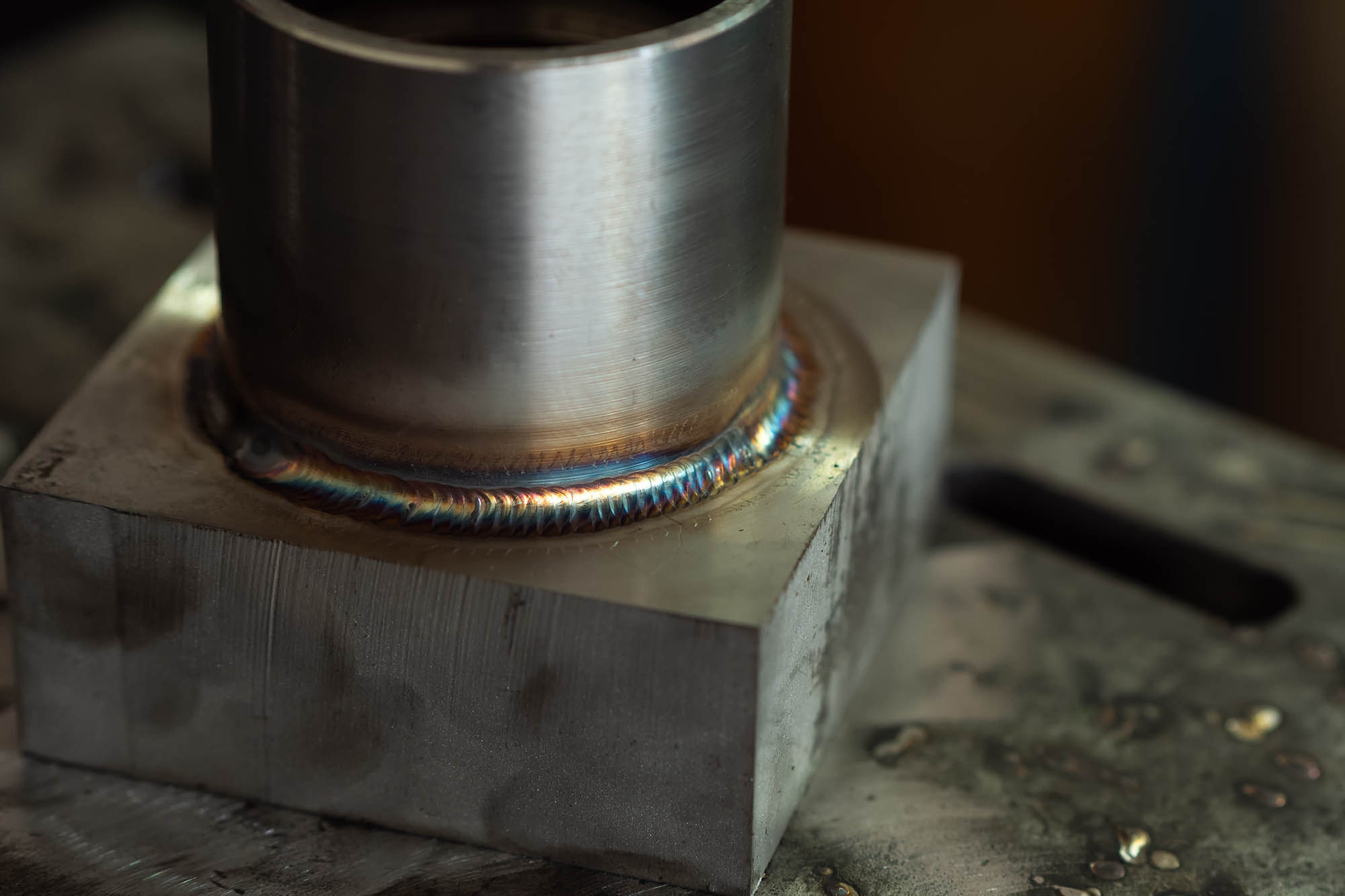
Aspects Affecting Porosity Formation
The occurrence of porosity in welding is affected by a myriad of variables, varying from gas protecting effectiveness to the intricacies of welding specification settings. Welding criteria, including voltage, existing, take a trip rate, and electrode type, likewise effect porosity development. The welding method employed, such as gas metal arc welding (GMAW) or secured steel arc welding (SMAW), can affect porosity development due to variations in warm distribution and gas protection - What is Porosity.
Impacts of Porosity on Weld High Quality
Porosity development considerably jeopardizes the structural integrity and mechanical residential properties of bonded joints. When porosity is existing in a weld, it creates voids or dental caries within the material, minimizing the general strength of the joint. These gaps work as anxiety focus points, making the weld much more prone to fracturing and failure under lots. The existence of porosity additionally weakens the weld's resistance to rust, as the caught air or gases within deep spaces can react with the surrounding atmosphere, bring about destruction with time. Furthermore, porosity can hinder the weld's capability to stand up to stress or impact, additional endangering the total advice high quality and integrity of the welded framework. In essential applications such as aerospace, automotive, or structural buildings, where safety and security and durability are vital, the destructive effects of porosity on weld quality can have extreme repercussions, highlighting the significance of minimizing porosity with correct welding techniques and procedures.
Strategies to Reduce Porosity
To boost the quality of bonded joints and make certain architectural honesty, welders and producers utilize certain methods focused on minimizing the formation of spaces and cavities within the material throughout the welding procedure. One efficient approach to lessen porosity is to make certain correct material preparation. This includes thorough cleansing of the base metal to eliminate any kind of pollutants such as oil, oil, or moisture that can add to porosity formation. Furthermore, using the proper welding criteria, such as the correct voltage, present, and travel speed, is vital in protecting against porosity. Preserving a constant arc length and angle throughout welding likewise assists minimize the probability of porosity.

Making use of the proper welding technique, such as back-stepping or utilizing a weaving movement, can additionally aid distribute warm evenly and minimize the chances of porosity formation. By executing these techniques, welders can effectively lessen porosity and generate high-grade welded joints.

Advanced Solutions for Porosity Control
Implementing sophisticated modern technologies and cutting-edge approaches plays a pivotal role in attaining remarkable control over porosity in welding processes. One sophisticated anchor service is using advanced gas mixtures. Securing gases like helium or a combination of argon and hydrogen can assist reduce porosity by giving far better arc stability and enhanced gas coverage. In addition, employing advanced welding techniques such as pulsed MIG welding or changed ambience welding can also aid minimize porosity problems.
Another sophisticated remedy entails the usage of advanced welding equipment. For instance, making use of visite site devices with built-in functions like waveform control and advanced source of power can improve weld top quality and reduce porosity threats. The application of automated welding systems with precise control over specifications can substantially reduce porosity flaws.
Furthermore, integrating sophisticated monitoring and inspection modern technologies such as real-time X-ray imaging or automated ultrasonic screening can aid in finding porosity early in the welding procedure, permitting immediate corrective actions. On the whole, incorporating these innovative services can considerably boost porosity control and boost the overall high quality of bonded components.
Verdict
To conclude, understanding the scientific research behind porosity in welding is essential for welders and fabricators to produce high-grade welds. By determining the elements affecting porosity formation and implementing strategies to minimize it, welders can boost the general weld high quality. Advanced services for porosity control can additionally enhance the welding process and ensure a strong and trusted weld. It is necessary for welders to constantly inform themselves on porosity and execute finest methods to attain ideal outcomes.